Kong[Moderator]
7855
Chopard Manufacture Visit Part 2(a)
Feb 24, 2009,23:32 PM
Continuation from Part 1 of Chopard Visit.
After the first day in Chopard at Geneva, the following day was to visit an important site.
A
site which Mr Karl-Friedrich Scheufele has worked to rekindle Chopard's
actual trade - watchmaking.
It is the 'return-to-root' location in the
Swiss Jura hills where Chopard watchmaking began - Fleurier, in
Val-delTravers.
That day, my good host, Mr.Patrick Wehrli arrived early and we set of at 7:30am.
The trip to Fleurier, from Geneva takes about 1.5 hour by car.
Some pics along the way ...

Up on the highway ....

Some houses and a small yard on my right ...

Cutting through a town and hills, then ...
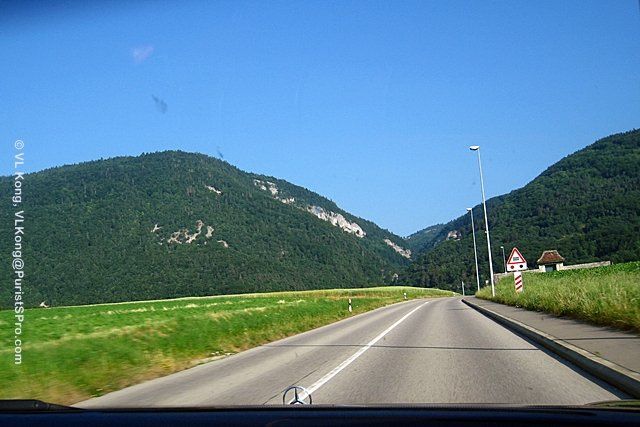
through a quiet road to nowhere ...

Then this interesting saw-tooth-chain rock formation.... understand from my army-trained host, this rock-chain is some
sort of a barricade to prevent the enemy tanks from crossing during last world war.
I think it is called Toblerone ... yes, like the popular chocolate
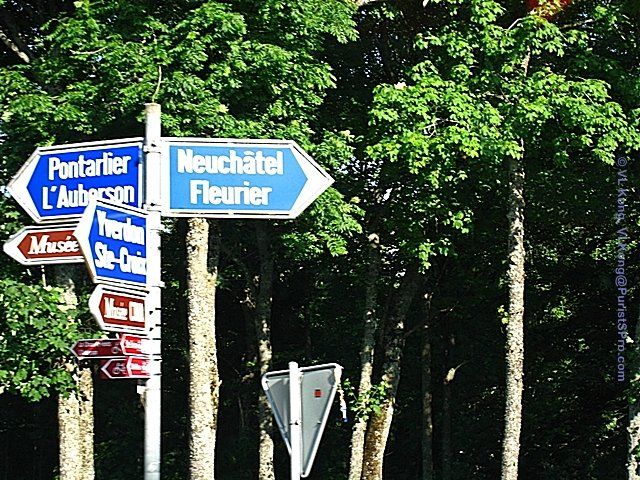
At 8:42am ...a sign!

Still not arrived yet...

A map from the Watch Valley to provide perspective, the location Fleurier and Geneva.
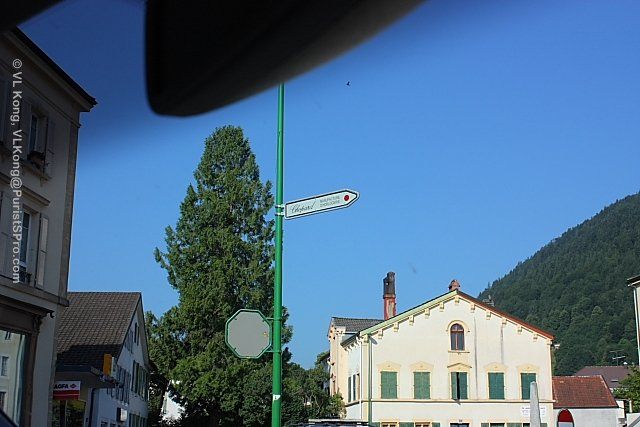
At 8:53am...saw the signage pointing to Chopard.

Passing by the extremely quiet town, no human in sight but really serene.

This was a picture of the building before ...the birthplace of the Chopard Manufacture since 1996.
Initially started with half a floor as more machinery were purchased, the expansion speeded up...eventually Chopard purchased
over the whole building in 2000 and did a renovation.
Total amount invested in the buildings, machinery and others since 1996 amounted to CHF30 Millions.

A minute later....the new Chopard Manufacture emerged !
Standing at the entrance, took several pics before entering the building ...

A hill on my right -side and a playground opposite the building....

To my left ...

The playground in front ...

The entrance to Chopard Manufacture

A 6-level building with a basement

The friendly receptionist ...greeted us..
Perlage pattern welcomes everyone at the front door

Followed by another framed message as a reminder or mantra to everyone... synonymous to L.U.C
Just my interpretation :
L.U.C ( as conceived by Karl-Friedrich Scheufele) to be positioned as a watch 'with substance that will last and enables
the adventure to go on' and it is dependent on the MOVEMENT. Precision is relevant here.
Staying just a while in the reception area, I could feel this venue is everything about horology, and time.
Of course, later we visit one of the ultimate 'time capsule' - the LUCEUM.
Opposite the frame is ....
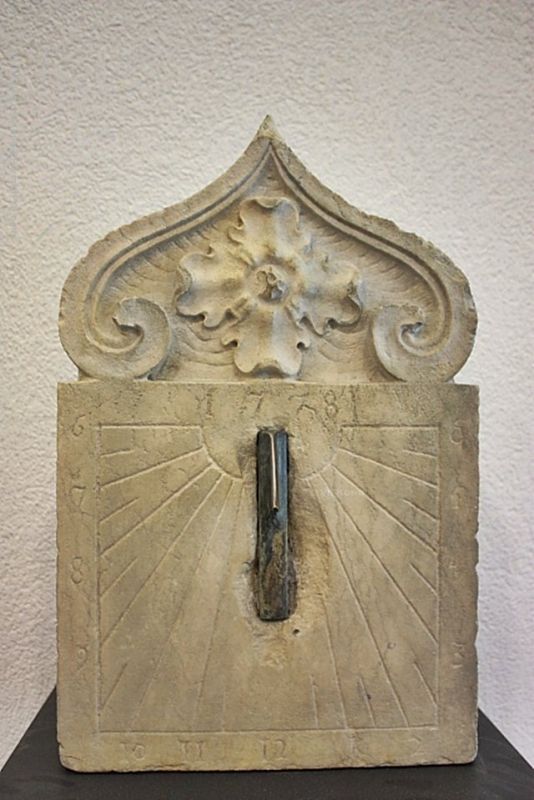
A 'Cadran Solaire , circa 1778' , a sun-dial

Behind the receptionist ... another nice piece ...did not manage to get the details.
Will look very good if this could be a miniaturized dial ...aged over time...
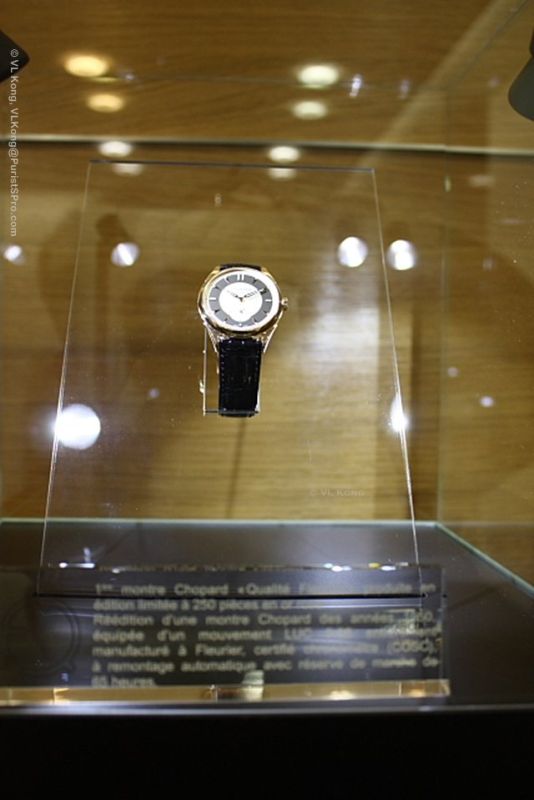
This piece L.U.C Qualite Fleurier (QF with Caliber 9.96) is relevant to this site, and it is a milestone for L.U.C.
The L.U.C QF commemorates the launch of the extremely stringent Haute Horlogerie Quality Certification by the
Fleurier Quality Foundation (FQF) in 2004.
More about the FQF later in Part 2B.
The excursion began with Patrick Wehrli leading the tour.....

The machining division

A very clean and tidy working environment.
This is very heavy investment.
3
top notch multi-axis Mill Turn machine centre with extremely high
precision specially for the precision, aerospace and watch industry.

The components fabricated at Fleurier are near to 85% to 90% of each movement/calibre requires ranging from the main plate,
all bridges, tourbillon cage, click spring, yoke spring and date disc. Earlier on, at Geneva plant, we have seen Chopard's
capabilities to design and develop own toolings to stamp their own casings.
To meet the Swiss Made criterias, Chopard easily surpasses the criterias.

Unfinished main plates

The unfinished main plate of the signature Quattro Double twin-stacked barrels (4 barrels) cut-out.

Unfinished carriage supposedly to hold the Variner Balance.

A
sample set indicating the progressive steps of fabricating the various bridges of the Quattro (lower row).
The above row is the main plate.
A few close up shots followed ....

The above are the barrel bridge, balance bridge and gear train bridge of the Quattro Calibre 1.98 .

Theses are 3 super hard and dense tungsten rotors which were machined out from these Multi-Axis MC.

This piece of speedster is a very advanced 6 axes machine. It can cut very complicated shape at great precision.

More machines on the other side...

Semi cut plates...pending for next operations.

Cutting in action with the coolant spraying onto the workpiece.

Another zoom out view.

Beside the machine is the automatic quick change tool-magazine.
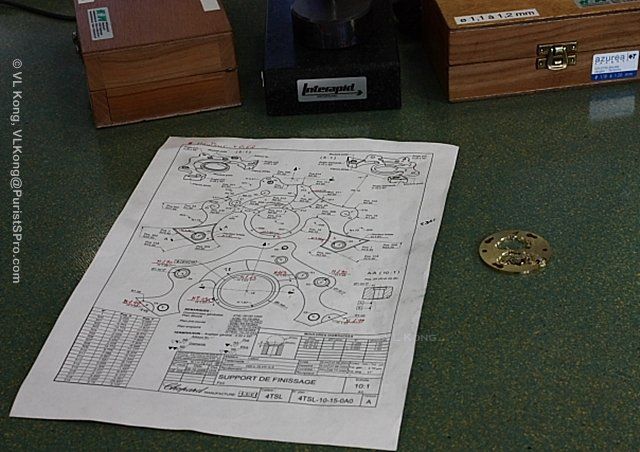
A drawing of a tourbillon bridge of Caliber 4T
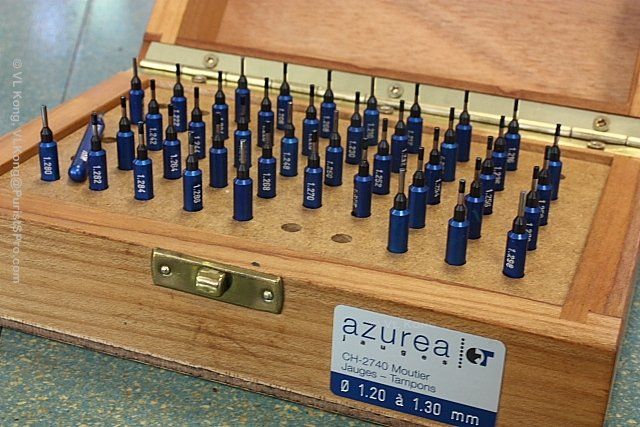
A box of 'GO' and 'No Go' gauges from diameter 1.200 to 1.300mm. Note it is to the 3rd decimal places. Each piece is
at an incremental 0.020 mm or 20 microns.

A digital depth gauge is used for more accurate readout.

As the components are small, naked eyes are not good enough for visual inspection. All parts to be examined under
a microscope.

Even better, a more sophisticated vision system matching the parts to the CAD drawings.

Parts are measured at a regular interval to ensure the dimensions are inside the controls.
In Chopard, I observed they implemented Statistical Process Control (SPC), which is not a surprised since this plant has
obtained
ISO 9001:2000 certification since 1998. That's besides the point, the SPC is implemented to
ensure parts
manufacturability and repeatability.
It is the first and foundational step to reliable movements and mastering the processes.

Each batch is considered one sub-lot , and accompanied by a ticket for traceability.

At the end of the room, there is a wire-cut EDM.
Typically
use to cut a contour in a workpiece. So it is mostly used to cut
precision stamping-die manufacturing and miniaturized
parts.

The wire (which use to cut) diameter is ranging from 0.02 to 0.30 mm. Very fine and delicate.

Saw the date-discs beside the wire-cut machine (with label "Good" & Defective").
Perhaps the date-discs are fabricated using this machine.

Another set of non-contact vision measurement system. It is neccessary for such miniature components.
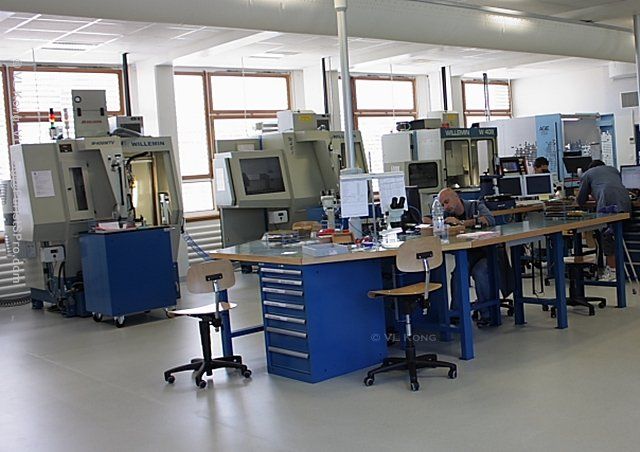
Leaving the super Machining Division ....
Next entering a quiet room....

Brushes, wood-sticks (like giant toothpicks) and microscope?

The specialist is doing manual deburring under scope.
Yes, even with high-tech machinery, burrs still occur. Its inevitable in cutting processes.
Woodsticks are used so as not to damage the brass parts.

A reference to the size of the parts the ladies could be working ... I placed a thin 0.3mm wire beside.
Observe the edges of the bottom piece with burrs. The piece above it, the edges and holes were completely deburred.
Notice the difference?

Some smaller parts require a special holder to grip.

After deburring, all parts are to be washed off the oil, contaminants and debris with this industrial cleaner.
This cleaning process is critical to the next...if the surface is not thoroughly cleanse, the plating would be affected.
Next we have a glimpse of the
Plating Section,

Full plating facility

It is reassuring to see the L.U.C has the in-house complex plating capability.
As good and well controlled processes ensure the durability of the plating.

A rhodium plating station.
Rhodium is important for white gold cases. Rhodium not only provides the mirror-shine surface, it is also resistant to
surface abrasion and chemical. However the control of the thickness is critical.
Thus it is great to have the plating process in-house as it can be tightly controlled internally.

Some gold-plated main-plates...
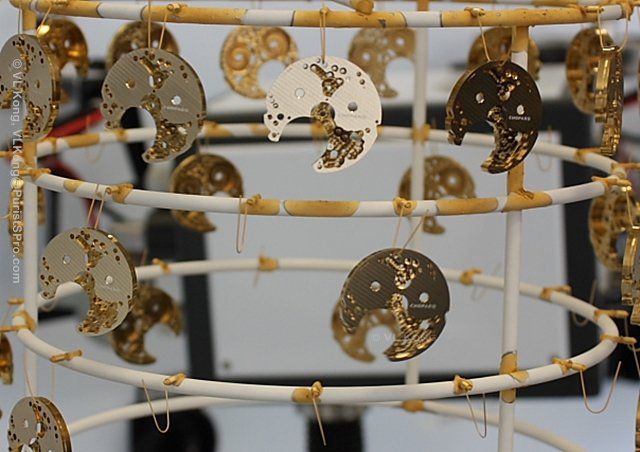
A closer shot ...
Next to the Movement Decoration Division Did you notice the below piece of bridge has gold-letterings on the a white rhodium surface?
This is another tedious process which gives the bridges a distinctive look with the bi-colour decoration step ...

Every
piece of bridges after gold-plated will be manually painted with a
special ink which acts like a resist or mask against the
next rhodium plating.
The tools are a microscope, ink, a thin brush (or a syringe) and most important the manual dexterity.

Masked with a black ink

Masked with a white ink

Unmasked pieces ....

Instead of brush, this is with a syringe ... each piece is carefully masked...

Some of the masked pieces, ready to be sent for nickel and rhodium plating. After which the masks will be stripped using
a solvent and then sent for cleaning again.
Continue with the next technique ... 
The scope of skills for the Movement Decoration

First stop, perlage or stippling (or circular graining)...a surface process to create continuous circles with arcs over-lapping
or just touching the centre of the next circle.
It
looks like simple process, however, to execute a quality perlage with
consistent overlapping requires great skill from the specialist.
Not
only consistent overlap, though the depth of the spindle is controlled,
the specialist has to pay detailed attention that equal
downward force is applied to produce consistent pattern cut and also to know
when to make adjustment when the stippling
tool wears.

The specialist has a jig to jog her piece from inside to outside perimeter.
Side-lights are mounted to assist her in proper alignment of the workpiece during stippling and also enable
her to see from the reflection in case the perlage pattern starts to thin down due to tool wears.